Although supply chains are at the core of an organization’s operations, it’s difficult to integrate them into a digital transformation initiative. According to McKinsey, the digitization of supply chains is at 43% — lower than any other function. This is largely due to siloed legacy systems, fragmented ownership, lack of universal data standards, budgetary preference for customer experience technologies, ROI skepticism and an illusion that legacy technologies are good enough.
What can be done? With global events highlighting the vulnerability of supply chains, now is the time for leaders to take the steps required to reach the next generation of supply chain management. What’s needed is ambition to take on the challenges that lie ahead.
Current supply chain challenges
There are two primary supply chain challenges that are driving the case for digitalization:
1) Supply chains are becoming increasingly complex
2) Existing technologies are no longer adequate to handle this complexity
Let’s look at both of these in more detail.
Increasing supply chain complexity
Complexity in modern supply chains is driven by many things, from changing customer preferences to market dynamics.
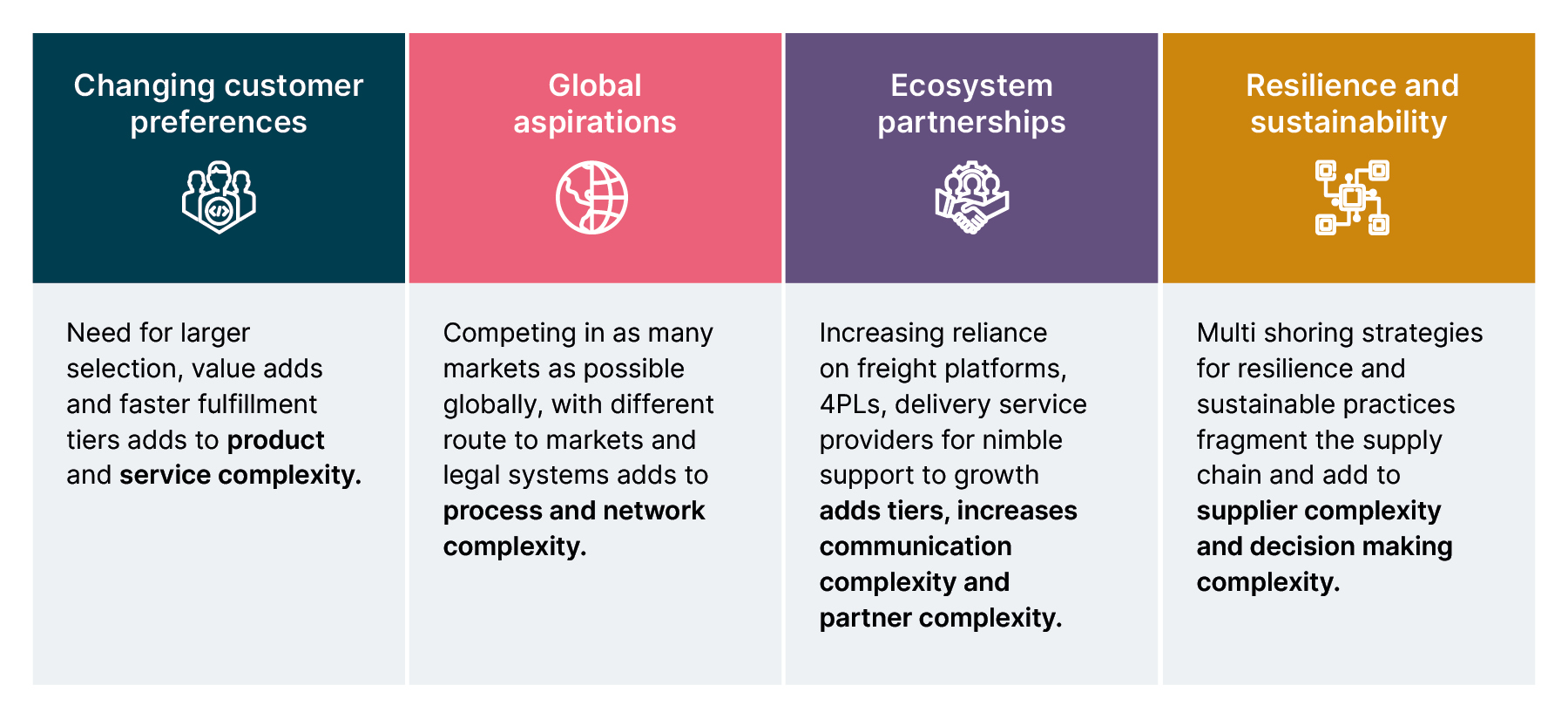
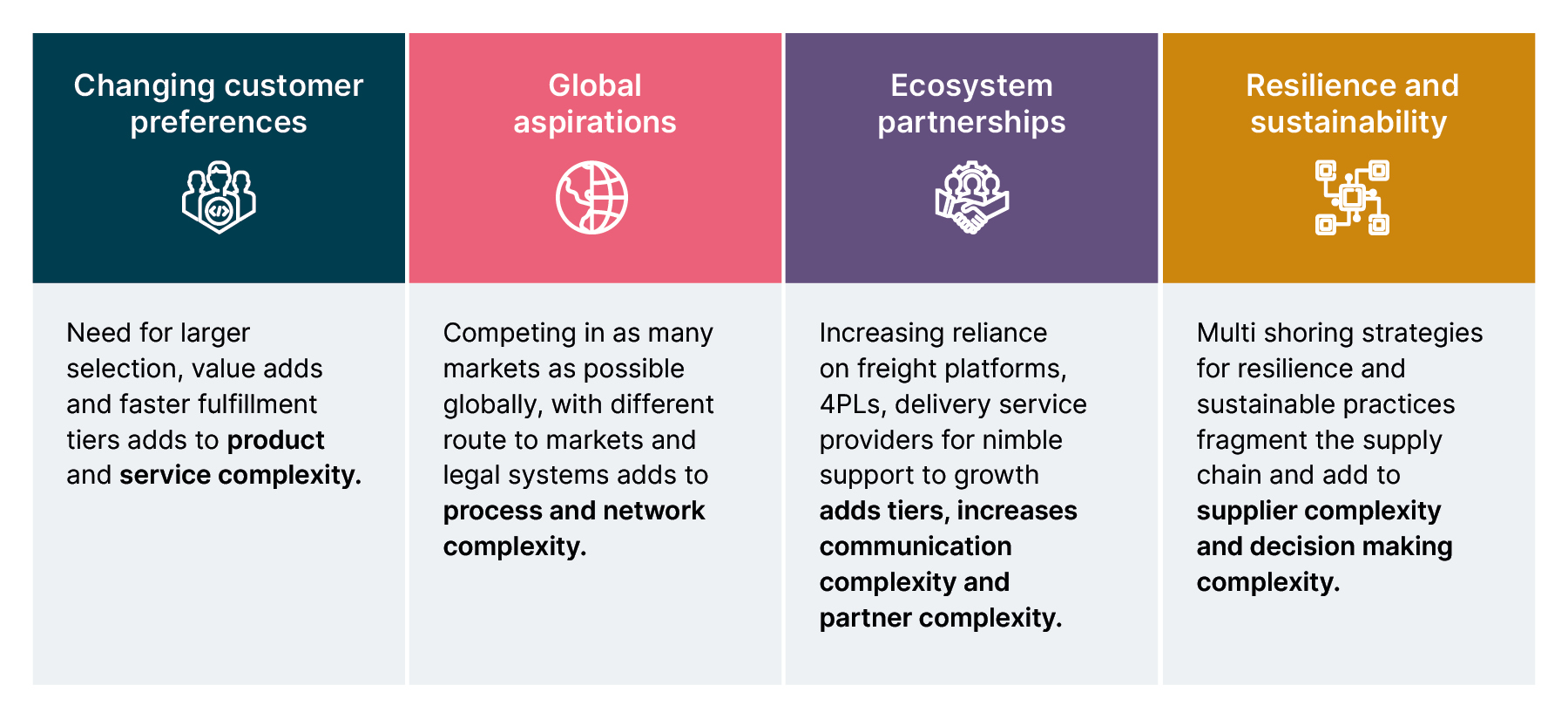
Handling this complexity requires near real-time visibility and oversight beyond organizational boundaries. It also demands exemplary forward planning with higher predictability, and effective communication across stakeholders to ensure the right decisions can be made quickly.
The challenge with existing technologies
Those challenges pose very intense demands on existing supply chain technologies. Although there has undoubtedly been innovation in this space — the deployment of specialized web-based ERP with add-ons for integrated planning applications and collaboration, for instance, and computer controlled mechanization — these technologies are both costly and complex, and don’t go that far in addressing current supply chain issues. Moreover, the tightly integrated monolithic nature of these systems mean it is also difficult for them to be adapted and scaled as necessary.
In addition, planning and execution are still divided by the ‘analog void ’. Current technology in supply chain management still relies on human faculties for much of the knowledge work needed to support these systems. With the increasing complexity of the supply chain, the effort needed to manage the scale and precision expected of the modern supply chains is now well and truly beyond human capabilities. The twin opposing forces of higher complexity and rigidity of older technology widen the gap in alignment between business needs and tech capabilities.
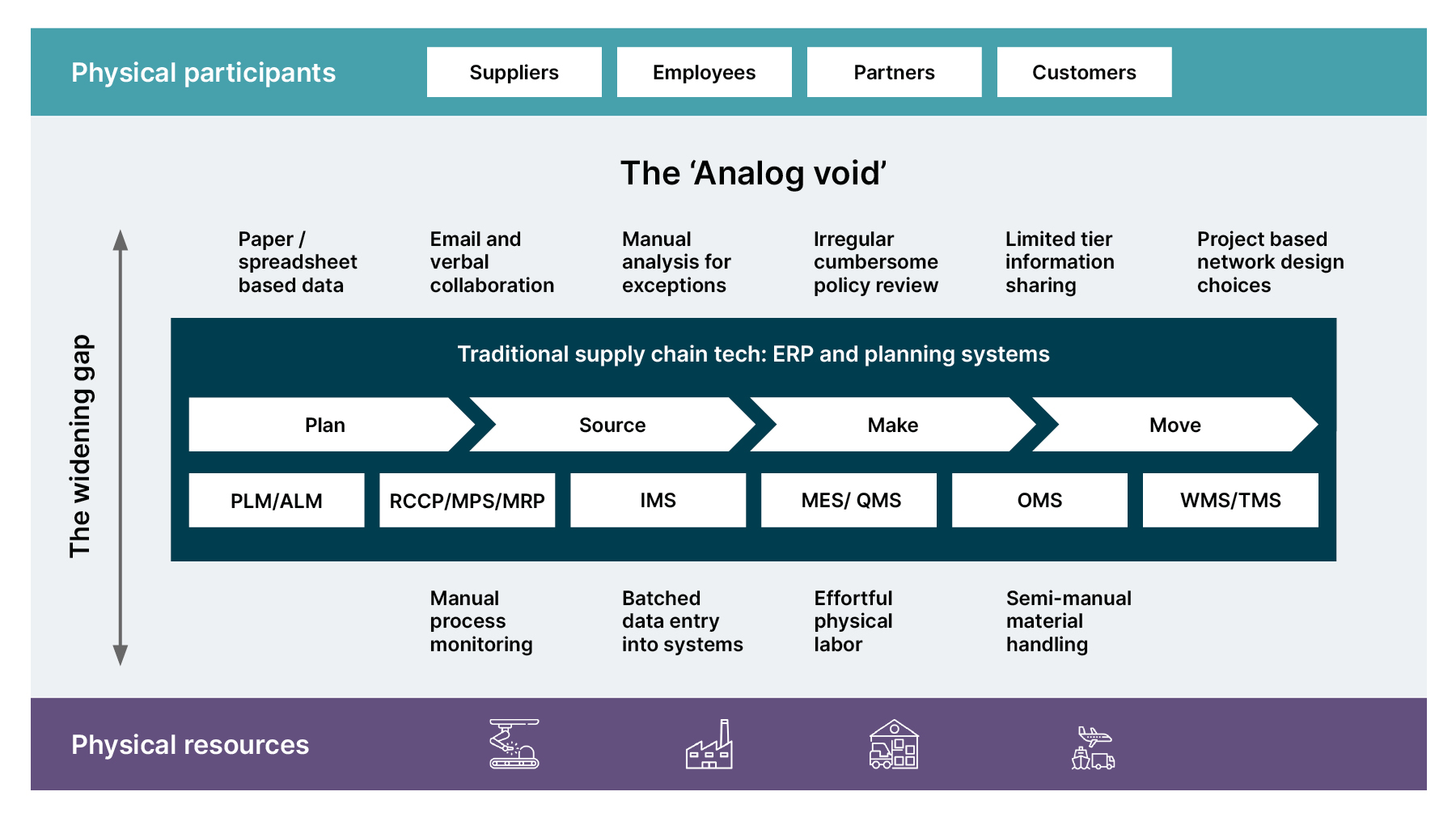
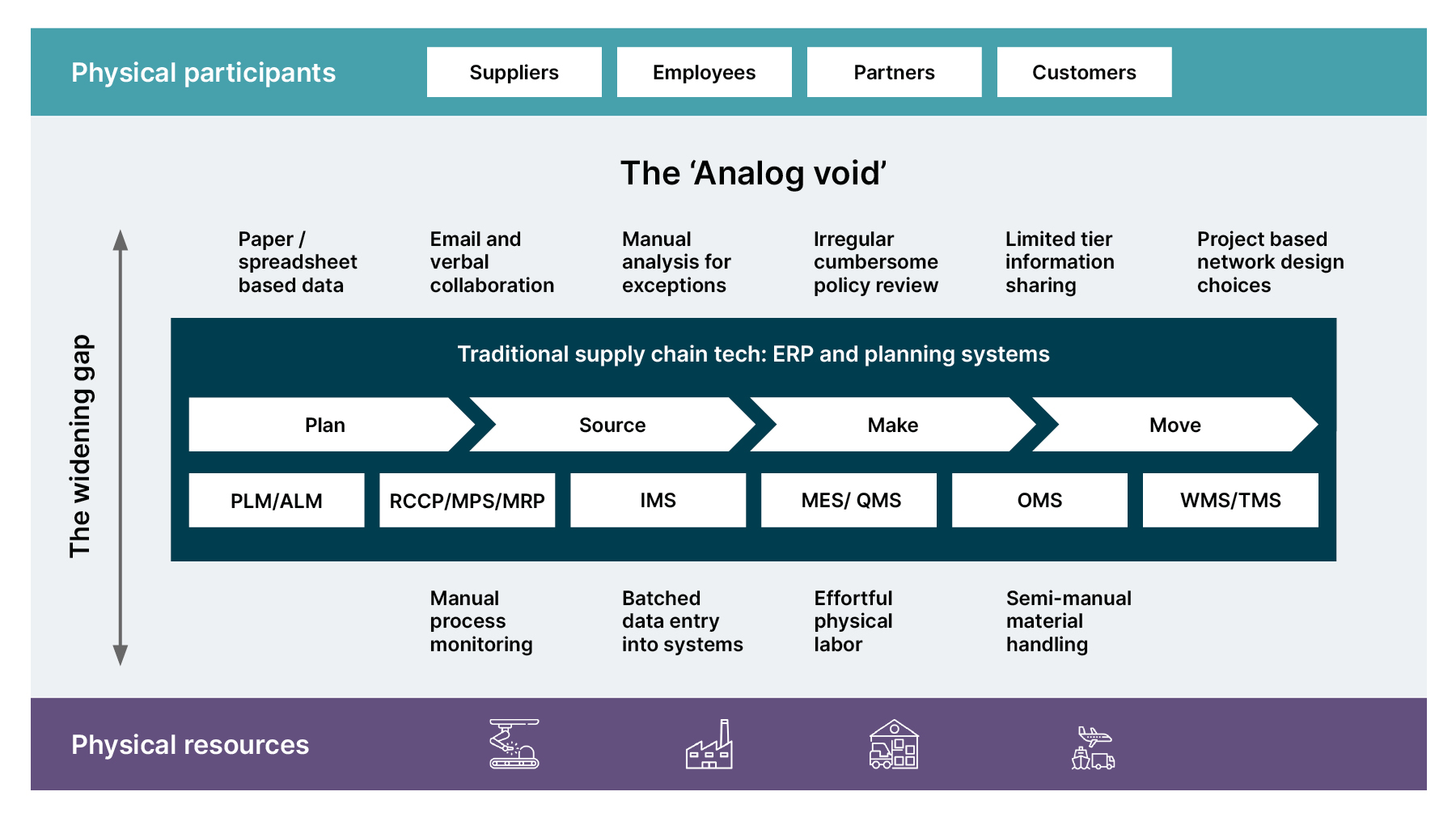
Given the heightened complexity of modern supply chains and the need for increasingly fast execution, this is a problem: what’s required can’t be done through manual human effort.
Digital transformation is thus now a strategic imperative.
The opportunity
There is immense value to be unlocked by targeting this analog void and suitably integrating modern digital technologies — cloud, IoT, big data, AI and machine learning — into supply chain operating models at all layers: from strategy to execution.
Strategy: Many organizations still continue to use a spreadsheet-based approach to supply chain modeling or hire advisory services for long-range decisions around network design, facility location and policy development. These decisions are rarely reviewed or updated. However, with the help of digital tools that enable things like advanced analytics and digital twin modeling, strategic decision-making can be built on even more robust foundations. It may even be possible to use machine learning to inform your approach to long-term trends to support planning for future scenarios.
Planning: There is a trend towards shortening planning cycles; the concept of continuous planning has been offered as a way of mitigating supply chain volatility. Because planning is primarily a collection of optimization problems, we are beginning to see AI/ML solutions being introduced to this space. Cloud APIs are also being used to extend the capabilities of core planning systems making direct participation of all partners possible in collaborative planning. Planning also involves dynamic data-driven scenario evaluation using various process parameters. It can, therefore, benefit from process virtualization and simulative analysis with the help of tools such as digital twins. Such innovations are likely to be at the core of the future of continuous planning.
Orchestration: A new class of digital solutions are helping bridge the gap between planning and execution. ‘Digital control towers’ that act as a single point of end-to-end oversight are an example. Control towers sense and curate signals from operations about volatility and disruption to trigger and orchestrate timely actions. Similarly, at a robotics level, organizations are also developing abstraction layers for future flexibility and interoperability between information systems and automation systems called multi-agent orchestration platforms.
Execution: Radio-frequency identification (RFID), telemetry and near-field communication (NFC) are today being embedded for monitoring not just the status and condition of materials but also workplace safety and operational health. It’s likely that many large enterprises will adopt smart warehousing, autonomous logistics and robotic industrial automation in the years to come. This has the potential to redefine the speed of execution and operational throughput. Even century-old companies are embracing change by robotizing frequent and ergonomically intense tasks in manufacturing and warehousing. This is bringing them closer to the vision of lights-out factories. E-commerce giants are innovating with goods-to-person robotics that can form the backbone of programs like same day and express delivery.
New frontiers in supply chain management: Emerging technologies
While several digital technologies finding active traction across the foundational supply chain areas have already been discussed above, there are other emerging technologies that have the potential to unlock value in the future (although the scale of their impact remains to be seen). A 2024 Gartner survey shows 64% of leaders of the supply chain organization are planning to implement or have implemented generative AI use cases, highlighting that there is an appetite to explore the potential of such a new and unproven technology. Some possible applications include use cases such as automating long tail supplier negotiation, planning assistants and summarization or translation of logistic documents.
Next, to make collaboration in logistics more secure, transparent and equitable, several efforts through alliances like Blockchain in Transportation Association and VAKT are being undertaken to mainstream application of Blockchain networks. Thirdly, there are also efforts to further automate facilities — we’re starting to see wider adoption of technologies such as indoor flying drones and real-time location systems (RTLS) based asset and workforce tracking. Similarly, in transportation, autonomous vehicles are actively being piloted to establish a path to viable scaling.
The table below outlines the various facets of supply chain management and how they will be impacted by different types of technologies.
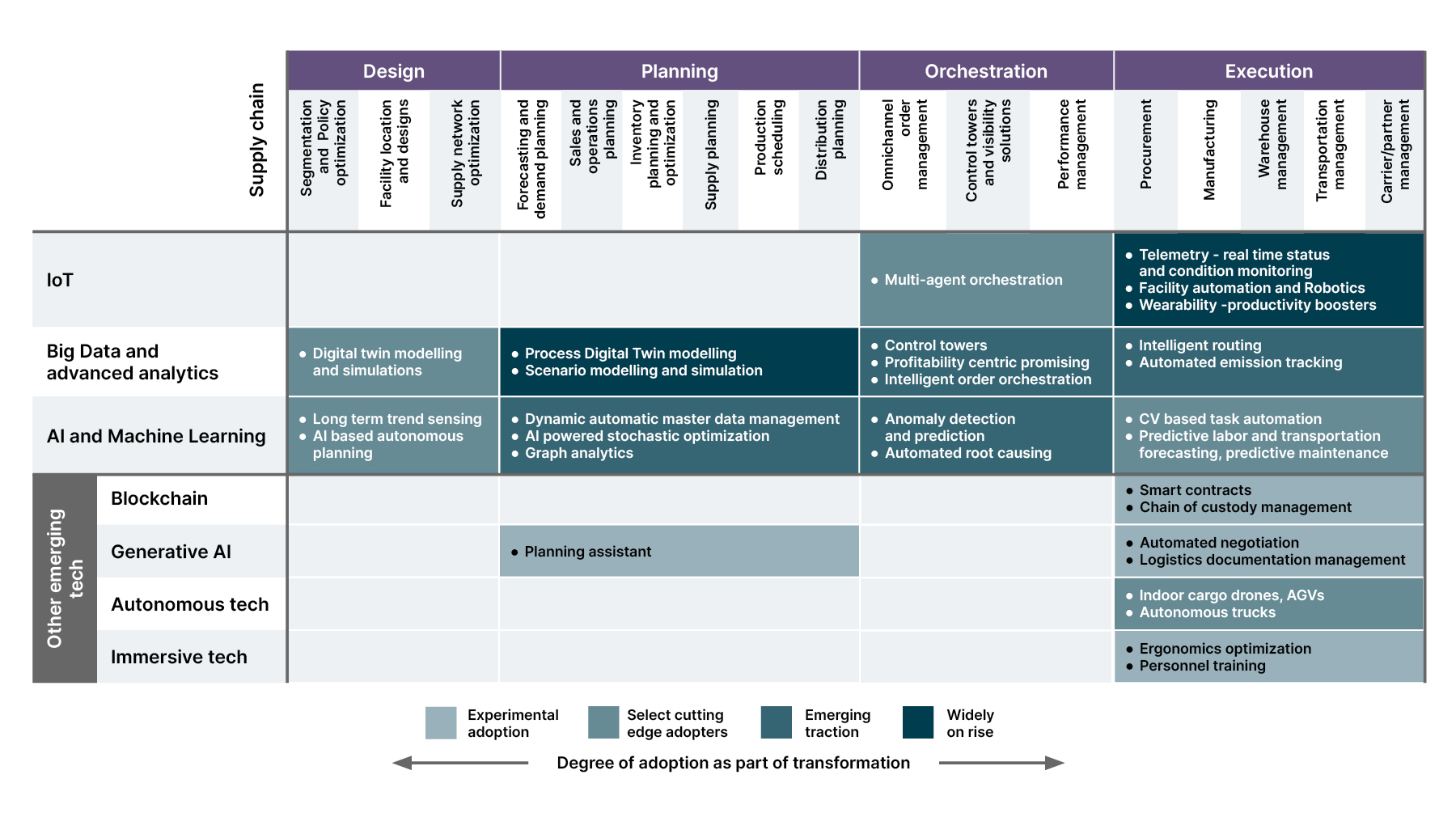
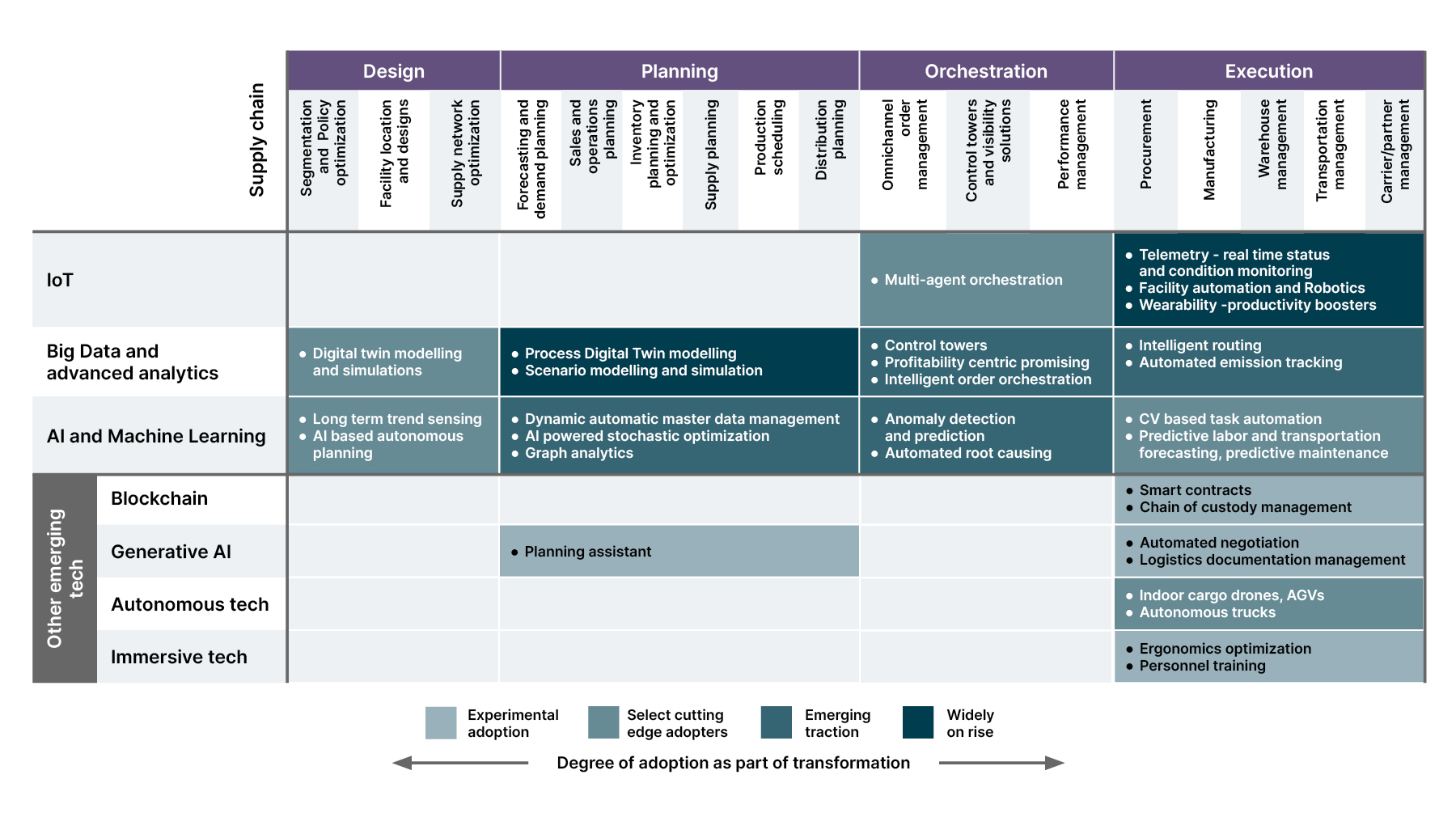
Seizing the digital opportunity
IDC research suggests 69% of organizations plan to accelerate digital programs in the supply chain suggesting transformations clearly cannot wait any more and emphasizing the risk of not treating this as a strategic priority.
To figure out where to start and what to do, organizations can begin by a dipstick assessment of how mature their digital adoption is on the adoption spectrum talked about in the previous section in the context of their industry, customer and competition. This will guide opportunity and potential to improve their current financial and operational performance through digital transformations. Such assessment should be fast-followed with aggressive and tightly integrated strategy by sorting their bets on impact, urgency and readiness of tech to formulate their own meaningful multi-year transformation roadmap.
Finally, technology transformation roadmaps must be drawn up alongside changes envisioned for operating models, team structures and people skills and not in isolation to maximize the benefits. Transformations can take several years, which means it’s important to continue to explore emerging technologies even as you implement changes; this ensures you won’t miss out on fast-moving innovations in the field. In conclusion, transformation isn’t a single big bang effort — it’s a deliberate strategic tool where you lead with technology at your core.
Disclaimer: The statements and opinions expressed in this article are those of the author(s) and do not necessarily reflect the positions of Thoughtworks.